Material Data Sheet
Heritage Sour Service - SM-C110
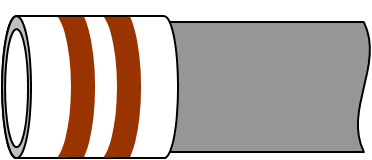
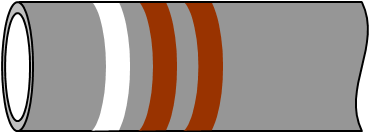
SM-C110 is a low alloy High Strength Carbon steel OCTG material suitable for severe Sour Service applications. SM-C110 is a Sulfide Stress Cracking (SSC) resistant material.
SSC failure mechanism is a form of Hydrogen embrittlement in combined presence of H2S, water and tensile stresses. SM-C110 was the first 110 ksi proprietary sour service material developed and its existence was recognized by NACE MR0175 in its 1996 revision through the addition of Para 10.2.2, for specific sour service application. SM-C110 benefits from Nippon Steel’s unrivaled know-how in manufacturing Sour Service materials since the 70’s and best-in-class quality control. SMC110 has no equivalent in API 5CT/ ISO 11960 grades and in order to achieve its superior Sour Service properties SMI applies a very strict QA/QC throughout its manufacturing route from Steel Making to Heat Treatment process.
Diameters: 2-3/8” to 16”
Weights: as per API 5CT/ISO 11960
Special application: Please contact Nippon Steel engineer, should You require specific size, weight, drift, or any other characterization.
- Proprietary SM-C110. TGP-2517 (latest revision)
- API 5CT / ISO 11960
- NACE MR0175 / ISO 15156-2
- API 5C1 / ISO 10405
- NACE TM0177
- VAM Book
Severe Sour service application corresponding to region 3, High H2S combined with low pH, as defined by NACE MR0175/ISO15156-2 (Fig 1). Its primary function is casing application.
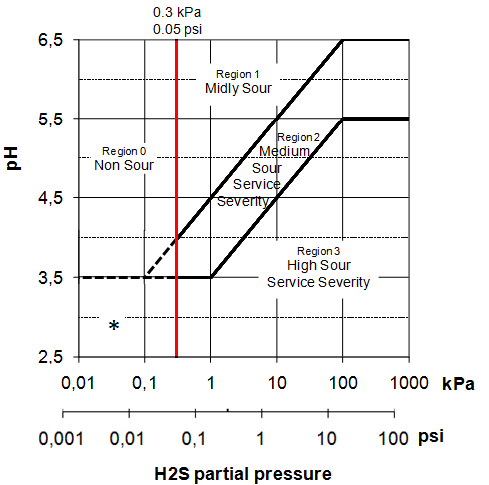
Fig. 1 : Sour Service regions in the pH vs H2S diagram
* Note : Even though this low pH corner is considered non-sour as far as H2S is concerned, caution needs to be exercised, as High Strength materials may become susceptible to Environmental Cracking (EC) even with no or very limited H2S.
There is a fair amount of confusion in relation to the H2S partial pressure limit applicable to 110 ksi sour service material. ISO 15156 / NACE MR0175 stance toward this type of materials may be overly conservative limiting their usage to either Region 1 or in any H2S partial pressure as long as these materials are exposed to temperature always exceeding 65°C (150°F). On the other end, the general interpretation is to consider these materials wrongly “full fledge” sour service with no H2S limit at all temperature. Nippon Steel, for the moment being, recommends usage of SM-C110 in H2S environments with H2S partial pressures up to 1 bar, at all temperatures.
For each manufactured SM-C110 heat, SSC resistance is verified through physical testing in accordance with NACE TM0177 method A, in solution A, using an applied stress of 85% SMYS.
As an option SM-C110 can be supplied with NACE TM0177 method D testing.
SM-C110 is a low alloy Sour Service material; consequently SM-C110 can be susceptible to metal loss corrosion if exposed to a dynamic acid gas containing environment, such as CO2.
For a more detailed assessment please contact Nippon Steel engineers.
PROCESS | DESCRIPTION |
---|---|
Steel making | Ladle refined, fully killed and vacuum degassed; continuously cast to a fine grained practice |
Pipe making | Seamless |
Heat treatment | Quenched and Tempered |
YIELD STRENGTH KSI |
TENSILE STRENGTH KSI |
ELONGATION % |
HARDNESS HRC |
TECHNICAL NOTE | |
---|---|---|---|---|---|
Min | Max | Min | Min | Max | |
110 | 125 | 115 | API Formula | 30.0 | 85% SMYS 1bar H2S, NACE A, Solution-A |
UNIT | 25°C | 50°C | 100°C | 150°C | 200°C | 250°C | |
---|---|---|---|---|---|---|---|
Density | Kg/m3 | 7750 | 7740 | 7730 | 7720 | 7700 | 7680 |
Young's modulus | GPa | 212 | 211 | 209 | 206 | 203 | 200 |
Poisson's Ratio | - | 0.30 | 0.30 | 0.30 | 0.30 | 0.29 | 0.29 |
Tensile strength de-rating | % | 100 | 96.3 | 94.3 | 95.2 | 95.2 | 95.2 |
Yield strength de-rating | % | 100 | 95.8 | 93.8 | 92.3 | 88.2 | 86.8 |
Thermal Diffusivity | x10-6 m2/s | 11.9 | 11.9 | 11.5 | 11.0 | 10.3 | 9.74 |
Heat Capacity | x106 J/m3 deg.C | 3.49 | 3.61 | 3.72 | 3.83 | 3.97 | 4.17 |
Thermal Conductivity | W/m deg.C | 41.5 | 42.9 | 42.8 | 42.1 | 40.9 | 40.6 |
Specific Heat | J/Kg deg.C | 450 | 466 | 481 | 496 | 516 | 543 |
Thermal expansion | x10-6 / deg.C | - | 12.5 | 12.3 | 12.4 | 12.6 | 12.8 |
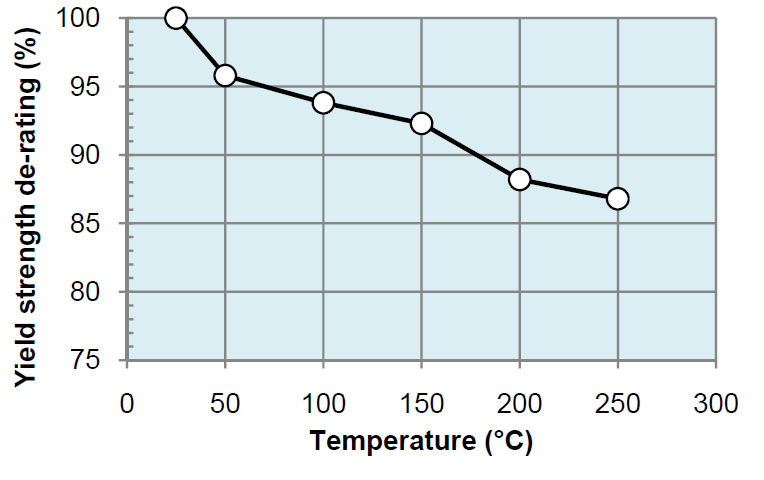
Temperature increase tends to minimize materials SSC susceptibility, and this tendency can be observed on API grades as well where, according to NACE MR0175 / ISO 15156-2, at higher temperature exposures high strength materials can be used in Region 3 of NACE MR0175/ISO15156-2 pH-H2S domain diagram (please refer to Fig 1).
Referring to API P110 grade in particular, this material can be used in high H2S environments if and only if the material is exposed to temperatures exceeding 80°C / 175°F (Fig. 2):
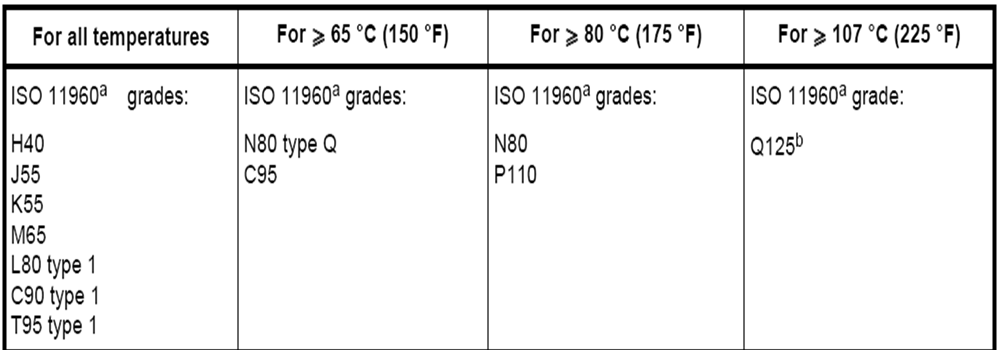
Fig. 2 : SSC Temperature thresholds for API Carbon steel grades according to NACE MR0175 / ISO 15156-2.
Figure 3 below shows the SSC results obtained on SM-C110 (1 bar H2Spp, NACE Method A, solution A) demonstrating the material's superior SSC resistance at ambient temperature, thus qualifying the material for all temperature applications. Nippon Steel SSC extensive research program on SM-C110 was performed using NACE Method A in Solution A, loading the material at ≥ 90% of Actual Yield Strength (AYS) within its Specified Yield Strength range, allowing a safety margin versus the guaranteed material SSC performances set at 85% of Specified Minimum Yield Strength (85% SMYS, NACE Method A, Solution A).
SM-C110 superior SSC performances have been confirmed as well on mill produced material as shown in Figure 3.
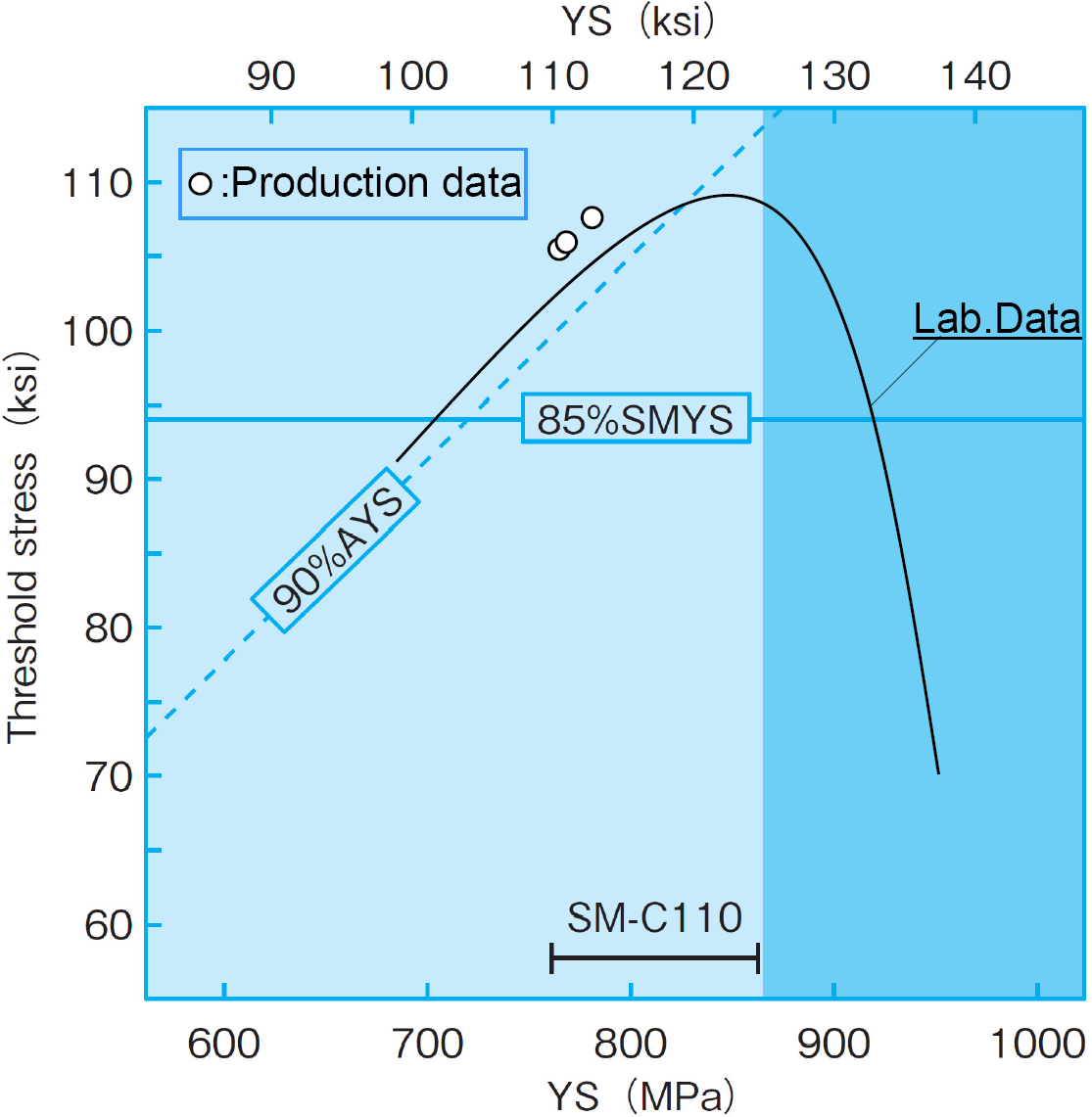
Fig. 3 : SM-C110 SSC susceptibility to material Yield Strength and applied threshold stress.
NACE Method A, solution A, 25 deg.C.
While the detrimental effect of actual material Yield Strength starts to be visible above 125 ksi, SM-C110 preserves its SSC resistance across the full range of its specified Yield strength range, as also shown in Figure 3.
For additional information about material performances please contact Nippon Steel engineers
A selection of critical applications of SM-C110 proprietary grade is shown below. These field records include SM-C110 used as intermediate and production casing:
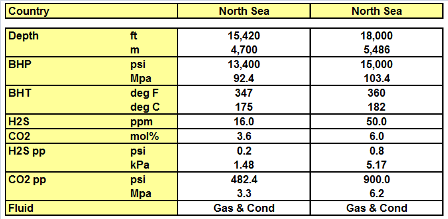
Health, Safety and Environment
While state-of-the-art HSE rules are applied throughout Nippon Steel manufacturing process, proprietary and specific HSE regulations shall be applied along the life cycle of the pipe until it reaches its final position in the well, according to each operator’s rules. This particularly applies to all phases of handling and transportation, assembly on the rig floor, and rig return if applicable. OCTG are heavy and by nature unstable. Special care shall be paid to potential risks of injury whenever handling OCTGs. Walking on pipes shall be avoided at all times. Usage of Personal Protection Equipments (PPE) is mandatory. Equipment and procedures will be established to capture the possible wastes generated during maintenance (cleaning, coating, doping) and disposed according to local regulations. This applies in particular to storage dope, running dope, or cleaning water wastes.
Best practices for transportation, handling and storage of OCTG in general are covered by ISO 10405 / API RP5C1. VAM Book is also a good source of handling practices for VAM connections. In addition to these general rules, specific care is recommended pertaining to SMC110, because improper handling could affect the material performances and by extension the corrosion resistance :
- Prevention of Spot Hardening
For more specific information please contact Nippon Steel engineers