Material Data Sheet
Sour Service - SM-125S
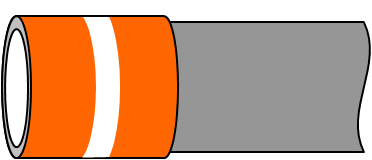
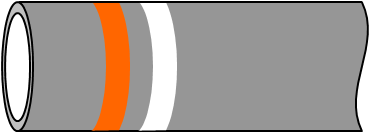
SM-125S is a low alloy High Strength Carbon steel OCTG material suitable for medium Sour Service severity applications. SM-125S is a Sulfide Stress Cracking (SSC) resistant material.
SSC failure mechanism is a form of Hydrogen embrittlement in combined presence of H2S, water and tensile stresses. Using cutting edge R&D technology, SM-125S was the first 125 ksi Sour Service material released in 2003. SM-125S benefits from Nippon Steel’s unrivaled know-how in manufacturing sour service materials since the 70’s and best-in-class quality control.
SM-125S has no equivalent in API 5CT/ ISO 11960 grades and in order to achieve its superior Sour Service properties Nippon Steel applies a very strict QA/QC throughout its manufacturing route from Steel Making to Heat Treatment process.
Diameters: 2-3/8” to 16”
Weights: as per API 5CT/ISO 11960
Special application: Please contact Nippon Steel engineer, should You require specific size, weight, drift, or any other characterization.
- Proprietary SM-125S. TGP-2214 (latest revision)
- API 5CT / ISO 11960
- NACE MR0175 / ISO 15156-2
- API 5C1 / ISO 10405
- NACE TM0177
- VAM Book
Medium Sour Service severity application corresponding to region 2, as defined by NACE MR0175/ISO15156-2 (Fig 1). Its primary function is intermediate and production Casing applciation.
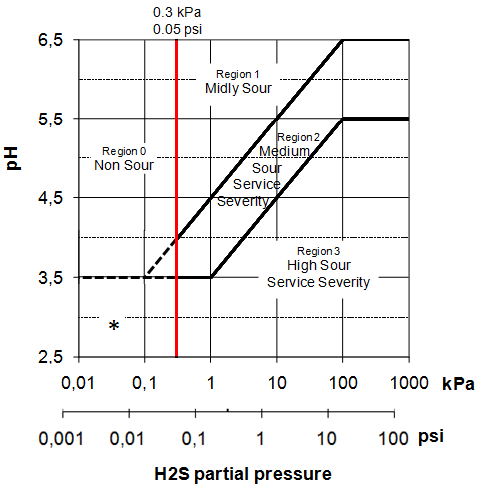
Fig. 1 : Sour Service regions in the pH vs H2S diagram
* Note : Even though this low pH corner is considered non-sour as far as H2S is concerned, caution needs to be exercised, as High Strength materials may become susceptible to Environmental Cracking (EC) even with no or very limited H2S.
For each manufactured SM125S heat, SSC resistance is verified through testing in accordance with NACE TM0177 method A, in solution B with 0.03 bar H2S, using an applied stress of 85% SMYS.
SM125S is a low alloy sour service material; consequently SM125S can be susceptible to metal loss corrosion if exposed to a wet dynamic acid gas containing environment, such as CO2.
For a more detailed assessment please contact Nippon Steel engineers.
PROCESS | DESCRIPTION |
---|---|
Steel making | Ladle refined, fully killed and vacuum degassed; continuously cast to a fine grained practice |
Pipe making | Seamless |
Heat treatment | Quenched and Tempered |
YIELD STRENGTH KSI |
TENSILE STRENGTH KSI |
ELONGATION % |
HARDNESS HRC |
TECHNICAL NOTE | |
---|---|---|---|---|---|
Min | Max | Min | Min | Max | |
125 | 140 | 130 | API Formula | 36.0 | Application: H2S < 0.03 bar* Tested: 85% SMYS, 0.03bar H2S, NACE A, Sol-B |
UNIT | 25°C | 50°C | 100°C | 150°C | 200°C | 250°C | |
---|---|---|---|---|---|---|---|
Density | Kg/m3 | 7800 | 7790 | 7780 | 7760 | 7750 | 7730 |
Young's modulus | GPa | 212 | 211 | 209 | 206 | 203 | 200 |
Poisson's Ratio | - | 0.30 | 0.30 | 0.30 | 0.30 | 0.29 | 0.29 |
Tensile strength de-rating | % | 100.0 | 98.6 | 97.2 | 96.8 | 96.1 | 94.8 |
Yield strength de-rating | % | 100.0 | 98.3 | 95.9 | 92.8 | 89.8 | 88.7 |
Thermal Diffusivity | x10-6 m2/s | 12.6 | 12.5 | 12.0 | 11.5 | 10.8 | 10.2 |
Heat Capacity | x106 J/m3 deg.C | 3.50 | 3.53 | 3.66 | 3.74 | 3.89 | 4.08 |
Thermal Conductivity | W/m deg.C | 44.1 | 44.1 | 43.9 | 43.0 | 42.0 | 41.6 |
Specific Heat | J/Kg deg.C | 449 | 453 | 470 | 482 | 502 | 528 |
Thermal expansion | x10-6 / deg.C | - | 12.0 | 12.3 | 12.6 | 12.8 | 13.0 |
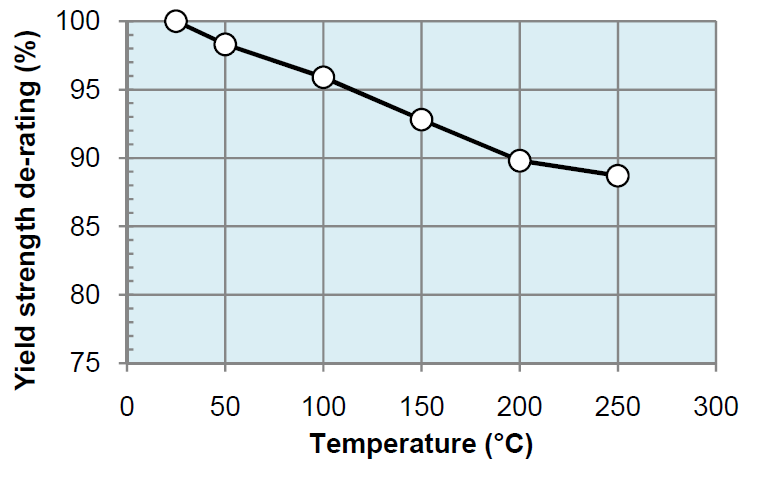
Conventional High Strength steel technology inherently features metallurgical limitations in being capable to deliver homogeneous and inclusions free materials (Fig.2 illustrates an example of High Strength steel inclusion). The main drawback of these limitations is that High Strength materials are highly susceptible to crack in H2S containing environments.
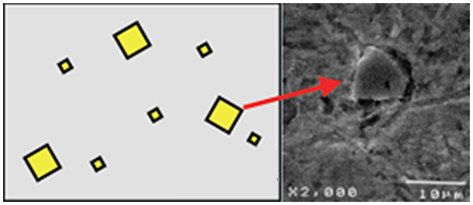
Fig 2 : Illustration of inclusion in conventional steel
Using Nippon Steel's prior manufacturing experience gained with the development of SM-C110 and based on the latest Sumitomo Research Laboratory cutting edge technology, specific efforts were put in place during SM-125S development to overcome these limitations. The final goal to reduce the dislocation density and control the carbide precipitation morphology was achieved through optimization in the material chemistry, heat treatment parameters and usage of inclusion morphology control technology.
Figure 3 first illustrates SM-125S pH/H2S domain diagram. "Reference" conditions (H2S partial pressure = 0.03 bar and pH = 3.5) used as a QC acceptance criteria for each manufactured SM-125S heat are indicated as well.
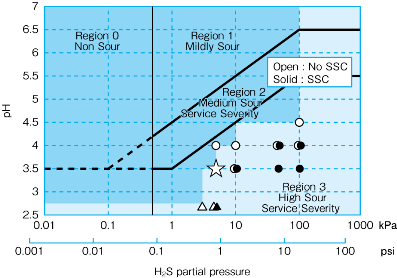
Fig. 3 : SM-125S SSC testing results in various combinations of H2S partial pressures and pH.
σappl=85%AYS, NACE Method A, solution-B, at 25 degC.
Note : Triangle marks are test results using NACE solution-A, while circle marks using solution-B.
Furthermore, Figure 3 demonstrates SM-125S increased domain of SSC resistance, in presence of higher H2S concentration combined with milder pH conditions. As part of this extended domain, SM-125S is suitable in conditions such as H2S partial pressure = 1 bar combined with pH = 4.5.
For additional information about material performances please contact Nippon Steel engineers.
A selection of critical applications of SM-125S proprietary grade is shown below. These field records include SM-125S used as intermediate and production casing:
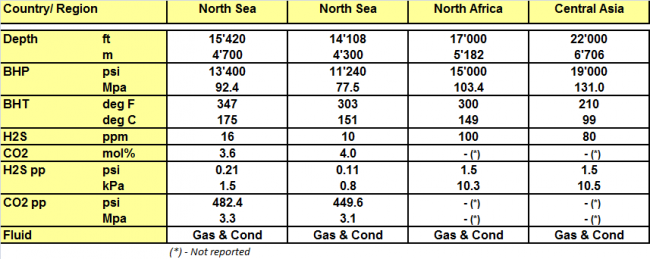
Health, Safety and Environment
While state-of-the-art HSE rules are applied throughout Nippon Steel manufacturing process, proprietary and specific HSE regulations shall be applied along the life cycle of the pipe until it reaches its final position in the well, according to each operator’s rules. This particularly applies to all phases of handling and transportation, assembly on the rig floor, and rig return if applicable. OCTG are heavy and by nature unstable. Special care shall be paid to potential risks of injury whenever handling OCTGs. Walking on pipes shall be avoided at all times. Usage of Personal Protection Equipments (PPE) is mandatory. Equipment and procedures will be established to capture the possible wastes generated during maintenance (cleaning, coating, doping) and disposed according to local regulations. This applies in particular to storage dope, running dope, or cleaning water wastes.
Best practices for transportation, handling and storage of OCTG in general are covered by ISO 10405 / API RP5C1. VAM Book is also a good source of handling practices for VAM connections. In addition to these general rules, specific care is recommended pertaining to SM125S, because improper handling could affect the material performances and by extension the corrosion resistance :
- Prevention of Spot Hardening
For more specific information please contact Nippon Steel engineers.